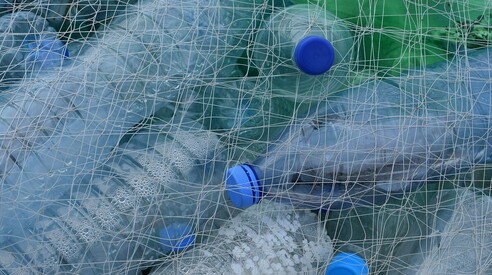
Foto Pixabay
Soluzione chimica
Il fondatore di Maire Tecnimont spiega come produce plastica riciclata a basso costo per tutti
Milano. “Trenta impianti come questo potrebbero essere la svolta decisiva per il problema dei rifiuti di plastica”. Nel suo ufficio in cima al grattacielo che domina la stazione Garibaldi di Milano, Fabrizio Di Amato mostra le immagini dello stabilimento costruito dal suo gruppo vicino a Brescia: qui gli scarti del materiale più odiato del momento si ritrasformano in materia prima e possono rientrare nel ciclo produttivo. Di Amato è il presidente e il fondatore del gruppo Maire Tecnimont, un colosso dell’impiantistica quotato alla Borsa di Milano, presente in circa 45 paesi, con un organico di circa 6.300 dipendenti, oltre a circa 3.000 professionisti della divisione elettro-strumentale. Costruisce o rinnova impianti di raffinazione e petrolchimici in giro per il mondo con l’obiettivo di renderli più efficienti. Nel 2018 ha realizzato un fatturato di oltre 3,6 miliardi di euro con 117,4 milioni di utili netti.
Appassionato di chimica (ha una laurea honoris causa conferitagli dal Politecnico di Milano), Di Amato spiega che oggi la plastica vergine deriva dal gas metano e dalla nafta: negli impianti petrolchimici si separano le singole molecole degli idrocarburi per “rimontarle” nei polimeri che diventeranno quelle piccole palline che poi riforniscono l’industria di trasformazione della plastica. “Il nostro obiettivo è realizzare degli impianti che invece di usare gli idrocarburi, utilizzano rifiuti di plastica”. Di Amato mostra due bocce piene di sferette di plastica: a parte il colore, sembrano identiche: “La differenza sta nel fatto che la prima è plastica vergine ricavata da idrocarburi di origine fossile, l’altra proviene dall’impianto di Brescia che ritrasforma i rifiuti di plastica in nuovi polimeri”.
L’impianto si trova a Bedizzole (Brescia), “il più avanzato ed efficiente in Europa nel riciclo di materiale plastico”, commenta Di Amato. “Si approvvigiona di scarti e materiali plastici post-consumo prevalentemente industriali. Può trattare ogni tipo di plastica ed è in grado di separare il materiale nei singoli polimeri. Dopo la selezione delle plastiche in ingresso per tipologia e colore e la loro triturazione in scaglie, viene effettuato il compounding, ovvero la fase di miscelazione che permette di mettere a punto il materiale, sotto forma di ‘palline’, con le caratteristiche adatte per la tipologia di oggetto che dovrà essere stampato dai clienti. La logica innovativa consiste nel partire dalle esigenze di formulazione dei clienti per produrre un composto che risponde alle richieste del mercato”. L’impianto è in grado di produrre oltre 40 mila tonnellate all'anno di polimeri riciclati: in altre parole, ridà vita all’equivalente della plastica gettata da un milione di persone in un anno, con un’efficienza di riciclo del 95 per cento.
“Grazie alla nostra leadership nella realizzazione di impianti di produzione di polimeri da idrocarburi, con la nuova società NextChem possiamo svolgere un ruolo da acceleratore dell’economia circolare”, aggiunge Di Amato. Che dice: “Noi facciamo polimeri da 70 anni e sappiamo che cosa serve al mercato. E’ questa la differenza tra noi e tra chi raccoglie e seleziona i rifiuti”. E se gli si chiede quanto costa la plastica che viene fuori dall’impianto di Bedizzole, convinti che sia più cara di quella vergine, la risposta è spiazzante: “La plastica che vede in questa boccia costa di meno di quella derivante dagli idrocarburi. Ed è di ottima qualità. Del resto, un barile di petrolio è più caro di un barile di rifiuti”.
L’impianto, spiegano alla Maire Tecnimont, è basato su tecnologie proprietarie e il processo di trattamento assicura un prodotto finito di qualità elevatissima, consentendone il suo utilizzo per manufatti in grado di entrare in mercati “premium” ad alto valore aggiunto (up-cycling). Partendo infatti dalle esigenze del mercato a valle, l’obiettivo è quello di produrre una plastica riciclata con caratteristiche chimico-fisiche e proprietà meccaniche in grado di colmare il gap qualitativo tra questa e la plastica vergine. Il risultato è che l’impianto guadagna senza usufruire di incentivi pubblici. “Il nostro piano – aggiunge Di Amato – è di licenziare a terzi la tecnologia per impianti di questo tipo, oppure proporsi per la realizzazione chiavi in mano. Il cliente-tipo è un produttore di plastica, un gruppo petrolchimico o una municipalizzata. Abbiamo già riscontrato un notevole interesse, potremmo costruirne subito una serie”. E alla domanda su quanti impianti di questo tipo sarebbero necessari in Italia per risolvere il problema dei rifiuti di plastica e il presidente risponde che “ne basterebbero una trentina”.