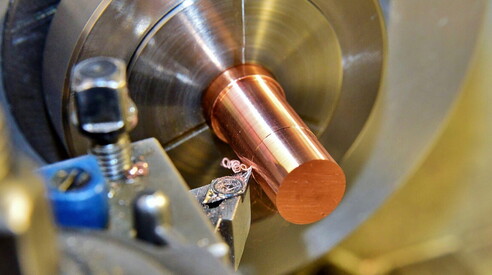
Foto Pixabay
Idee per aiutare i “sarti” della meccanica ad innovare il manifatturiero italiano
Un’industria della macchina utensile competitiva è presupposto indispensabile per assicurare al paese un sistema competitivo. La proposta di introdurre un Pacchetto unico per la crescita di impresa
Pubblichiamo l'intervento di Alfredo Mariotti, direttore Ucimu-Sistemi per produrre al Festival Città Impresa: Industria 4.0 dello scorso 9 novembre.
Grazie dottor Firpo. Signore, Signori, buongiorno.
permettetemi di salutarvi a nome di Ucimu-Sistemi per produrre, l’associazione dei costruttori italiani di macchine utensili, robot e automazione, che conta oggi 230 imprese associate in rappresentanza di più del 70 per cento del made in Italy settoriale.
Base per la quasi totalità dei processi produttivi, le macchine utensili per la lavorazione dei metalli e i sistemi di automazione sono definiti tecnologie abilitanti poiché abilitano l’innovazione di gran parte delle filiere manifatturiere, trasferendo innovazione, appunto, ai processi e ai prodotti che con essi vengono realizzati: dall’automotive all’aerospace, dalla meccanica generale all’energia, dall’elettrodomestico all’arredamento, dal biomedicale alla farmaceutica fino ad arrivare al machinery.
Un’industria della macchina utensile competitiva è presupposto indispensabile per assicurare al paese un sistema manifatturiero competitivo, che sia quindi in grado di recitare un ruolo di primo piano nello scenario internazionale.
E l’Italia può contare su un’industria di settore forte, caratterizzata da una solida e lunga tradizione, espressione di una miriade di imprese, tutte per lo più Pmi a gestione e conduzione familiare, che da semplici officine meccaniche si sono trasformate in aziende superspecializzate.
Con 400 imprese, 32.000 addetti e una produzione che nel 2018 si è attestata a 6,8 miliardi di euro, l’industria italiana di settore occupa da sempre posizioni di testa nelle classifiche mondiali ove risulta quarta tra i produttori e terza tra gli esportatori.
Riconosciuti come i sarti della meccanica, gli imprenditori di questo settore - che nell’accezione più ampia fattura quasi 10 miliardi di euro - guidano aziende che, in particolare nell’ultimo quinquennio, hanno lavorato intensamente allo sviluppo di soluzioni sempre più integrate e dotate di sistemi digitali per l’interconnessione e la gestione dei dati. Questo anche in risposta alle richieste dei clienti, stimolati a investire in tecnologie di ultima generazione anche dalla disponibilità dei provvedimenti 4.0 messi in campo dalle autorità di governo con i Piani Industria e Impresa 4.0 alla cui stesura ha partecipato anche Ucimu-Sistemi per produrre.
Insieme a Stefano Firpo, allora al ministero dello Sviluppo Economico, e insieme a numerose altre organizzazioni, abbiamo infatti partecipato attivamente alla definizione di questi Piani che hanno contribuito, in modo determinante, non solo a dare una scossa agli investimenti in nuove tecnologie di produzione, ma anche e soprattutto a stimolare e sostenere la trasformazione in chiave digitale dell’industria manifatturiera italiana che comporta anche una profonda trasformazione anche organizzativa delle aziende.
La validità di questi strumenti, insieme alla scelta di introdurli a partire dal 2015, quando il mercato italiano era tornato ricettivo, ha reso i Piani Industria/Impresa 4.0 realmente interessanti per un buon numero di imprese italiane che, dopo anni di astensione, sono tornate a investire in nuove tecnologie.
La conferma di questo ci è data dall’andamento dell’indice trimestrale degli ordini raccolti da Ucimu-Sistemi per produrre che è considerato a tutti gli effetti il misuratore dell’efficacia degli strumenti messi in campo dal Governo con i Piani Industria 4.0 e poi Impresa 4.0.
A partire dal 2015 l’indice degli ordini raccolti sul mercato interno è tornato a crescere in modo sostenuto, mettendo a segno, nel 2016 e nel 2017, risultati da record per poi cominciare a segnare il passo nel 2018.
Grazie ai provvedimenti di incentivazione, l’Italia è salita dal sesto al quinto posto nella classifica mondiale dei paesi consumatori di macchine utensili e soprattutto è stata investita da un profondo processo di trasformazione industriale.
Il risultato, ancora parziale, è che oggi il paese può contare su fabbriche e stabilimenti dotati di tecnologie di ultima generazione, conditio sine qua non perché il made in Italy resti competitivo rispetto all’offerta dei competitors esteri o addirittura migliori il proprio standard.
Secondo la ricerca congiunta realizzata da Confindustria e ministero dell’Economia e delle Finanze, presentata nella primavera scorsa, si stima che questo processo abbia riguardato 10 miliardi di investimenti per lo più legati a prodotti in metallo e meccanica strumentale. Un risultato interessante, questo, ma ancora insufficiente rispetto alle necessità del nostro sistema produttivo.
Nel 2018, a distanza di circa due anni dall’introduzione dei provvedimenti 4.0, Fondazione Ucimu ha condotto un’indagine sull’utilizzo degli incentivi di super e iperammortamento da parte delle imprese italiane.
Dai risultati dell’indagine condotta su un campione rappresentativo di 200 imprese è emerso che, a metà 2018, solo il 46,5 per cento delle aziende aveva usufruito degli incentivi, preferendo acquisire macchine dotate di tecnologie digitali, dunque in regime di iperammortamento. Buona parte di queste imprese dichiarava di essere intenzionata a fare nuovi investimenti. Di contro la ricerca ha dimostrato che più della metà delle imprese non era stata lambita dalla quarta rivoluzione industriale e, di queste, la grande maggioranza si diceva non intenzionata ad investire in futuro.
Sebbene queste rilevazioni risalgano a poco più di un anno fa, considerato il rallentamento della raccolta ordini interni, il cui calo è ormai registrato da 6 trimestri, è evidente che il processo di trasformazione dell’industria in chiave digitale sia soltanto avviato (e certo non concluso).
L’Italia ha bisogno di consolidare e incrementare il valore della sua produzione manifatturiera preservando le sue aziende, il know how e il lavoro.
E per fare ciò occorre una politica industriale ragionata che preveda, come fatto negli anni passati, un piano corposo e strutturato di provvedimenti per l’innovazione che abbiano validità di lungo periodo.
Pensiamo ad un Pacchetto unico per la crescita di impresa, strutturale, liberato cioè dalle annuali attese e incertezze legate alla possibile riconferma, o meno, di ciascuna delle misure in esso inserite.
Il Pacchetto per la crescita di impresa dovrebbe sommare in sé tutti i vantaggi fiscali legati a ricerca e sviluppo e a superammortamento e iperammortamento strumenti che hanno dimostrato la loro validità e per questo vanno preservati.
In particolare, da un lato, l’iperammortamento dovrebbe avere una durata almeno triennale, dall’altro, il superammortamento dovrebbe essere affiancato, per poi essere sostituito, dalla revisione dei coefficienti di ammortamento attualmente fermi al 1988 e per questo non più adeguati alle esigenze del mercato.
Queste misure sono indispensabili per sostenere il prosieguo della trasformazione del manifatturiero che, con specifico riferimento al settore delle macchine utensili, si sta sviluppando lungo 4 diverse direttrici che permettono, e permetteranno, all’offerta italiana di crescere oltre la sartoria continuando a incrementare il valore aggiunto della propria offerta.
La prima direttrice è senza ogni dubbio la digitalizzazione che si realizza con un’integrazione sempre più intensa tra sistemi IT e IOT e i macchinari.
Legata a questa c’è l’analisi e la gestione dei dati raccolti dalle macchine tra loro interconnesse che è presupposto per una serie di attività che di fatto rendono la fabbrica e la produzione intelligente. Penso a controllo a distanza, manutenzione predittiva, intervento da remoto ma anche alla gestione delle risorse, degli approvvigionamenti, alla customizzazione, alla logistica automatizzata…
Queste tecnologie favoriscono l’approccio alla produzione secondo i principi di sostenibilità che sono poi la base per lo sviluppo di economie green. Terza direttrice di sviluppo.
Sempre di più le macchine utensili italiane sono soluzioni pensate per garantire produzioni sostenibili, tema a cui dedicheremo la prossima edizione di BI-MU, biennale della macchina utensili in scena nell’ottobre 2020 a fieramilano Rho. In particolare questa direttrice si concretizza nello sviluppo di sistemi di produzione in grado di assicurare gestione sostenibile dei cicli produttivi della fabbrica a tutto beneficio della redditività aziendale, che corrisponde alla sostenibilità economica, della sicurezza, che si concretizza nella sostenibilità sociale, e della gestione ottimale delle risorse, che è sinonimo di sostenibilità ambientale e risparmio energetico
Ultima direttrice è la servitizzazione che interessa e interesserà sempre di più anche il settore delle macchine utensili. In linea con la tendenza alla smaterializzazione dell’economia, anche grazie, ma non solo, alle tecnologie 4.0, i costruttori italiani di macchine utensili potranno offrire insieme alla macchina un pacchetto di servizi basati su meccanismi pay per use o renting che già vengono utilizzati in altri settori e che, per loro natura, sono altamente remunerati a tutto beneficio della redditività aziendale.
È evidente che per sostenere queste sfide le imprese del settore siano impegnate con sforzi economici rilevanti ma altrettanto rilevanti sono gli sforzi da sostenere in fatto di sviluppo delle competenze del personale affinché risponda alle esigenze delle nuove fabbriche.
Per questo è necessario proseguire anche nel 2020 con i provvedimenti a sostegno della formazione 4.0 In particolare chiediamo che il provvedimento del credito di imposta per la formazione - come già più volte ribadito - sia rivisto.
Attualmente il credito è calcolato solo sul costo del personale impegnato nella formazione per le ore di aggiornamento svolte. La parte più consistente dei costi della formazione aziendale è invece rappresentata dal costo dei formatori: occorre includere quella voce di spesa nel calcolo del credito di imposta perché si tratta dell’aspetto più oneroso, specialmente per una Pmi.
Altro tema è quello dei giovani che devono essere preparati secondo competenze trasversali.
Nonostante un tasso di disoccupazione giovanile in Italia superiore al 30 per cento, nonostante il nostro paese sia il paese europeo con il maggiore numero di Neet, ovvero di giovani tra i 18 e i 24 anni che non hanno un lavoro e non sono all’interno di percorso di studi, i costruttori di macchine utensili incontrano grandissima difficoltà nel reperire figure professionali adeguate quali: meccatronici, elettronici, informatici ed esperti in tecnologie della produzione.
Sono purtroppo ancora troppo pochi i ragazzi che scelgono questi percorsi scolastici, specifici per le professioni legate al mondo dell’automazione e della meccanica di precisione.
Ucimu-Sistemi per produrre è, da sempre, impegnata in prima linea per facilitare l’avvicinamento dei giovani al settore attraverso la realizzazione di azioni concrete. Tra le numerose iniziative particolare intensità ha assunto negli ultimi anni proprio la collaborazione con gli ITS che - lo ribadiamo da tempo alle autorità di governo - devono crescere in numero soprattutto nelle aree industrializzate del paese così da poter coprire la domanda di lavoro espressa dalle aziende.
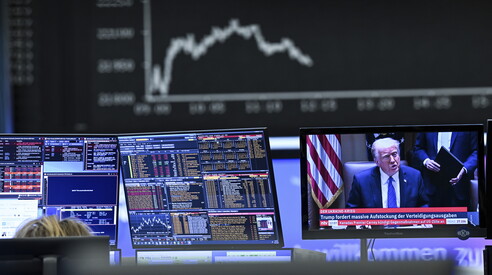
Altro che Liberation Day.
Trump nemico delle borse. Crolli in tutto il mondo a causa dei dazi
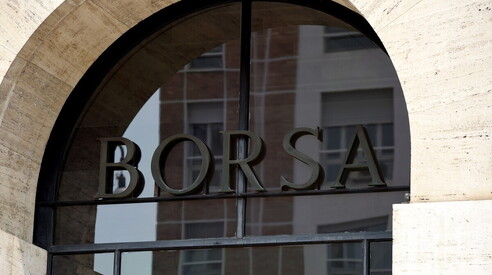
La reazione dei mercati
I dazi di Trump pesano sulle borse europee, ma danneggiano anche l'America
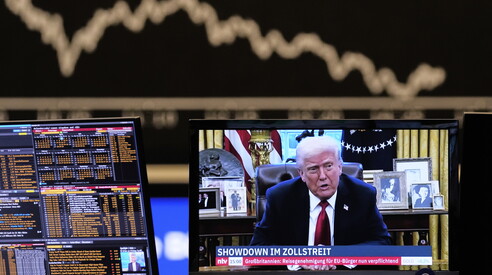